Ocotlan de Morelos, Mexico: Steel worked as in 16th century Toledo, Spain
Updated: I've edited the price on the big Bowie shown in the photos twice. I think I've got it right. I reduced the prices a lot . . . a whole lot. Also, I left out the final sharpening step. I should be stropped for that. Please scroll down.
This art of knife and sword making gets pretty complex, so I’m going to break it down into 3 posts. The first will introduce one of Mexico’s finest sword and knife makers and some of the basic rules to remember when buying a fine knife or sword.
One can purchase some of the finest knives and swords made anywhere in the world in Mexico. One can also purchase junk. You’ve got to know what you’re doing.
There are 3 different basic types of knives and swords being sold in the markets in Mexico.
The first and most common blade found in the Mexican markets is the chrome plated blade. These are everywhere. Beware. They are only good for a few years of hanging on your wall or sitting on your desk. They are useless for anything else. The steel is usually junk metal, sometimes only iron. The blades are cut and polished, then given a thin "flash" chrome job. To be fair, some of the knife makers do load on the nickel and chrome a bit heavier, but the knife is still no good for any practical use.
Also, if you know anything about electroplating, chrome plated steel begins to immediately destroy itself, bit by bit, as soon as it comes out of the last rinse tank. The layers of dissimilar metals (copper, nickel and chrome) pass a minute electrical charge between them, just like a battery does, which attacks the layers of metal and eventually will eat holes through each layer. There is no way to stop this electrolytic action.
The second type is the stainless steel knife or sword. These blades are very nice, but because of the cost of stainless steel, much of the cutting and forming of the blades, hilts, handles and pommels is done with machines. This helps to keep the cost down. Also, the stainless steel blades are softer and will not hold an edge like a hand tempered blade.
I have owned a very good Mexican stainless steel blade that was quite serviceable. I had to sharpen it before every use but I was satisfied with its performance - that is until I got my hands on a hand made and hand tempered blade. There is no comparison.
The third, and the very rarest, are the hand worked, hand tempered and hand sharpened and polished steel knives and swords. These are very hard to find. But when found and purchased, they are among the finest and most serviceable cutting blades that money can buy. And when made by an artist with almost 500 years of history behind him, the resultant blade is a keepsake as well as a valuable tool.
These hand formed and hand tempered blades require a minimum of maintenance. After buying one and using it for awhile, I realized that I spent far less time maintaining the hand tempered steel knife than I did in repeatedly sharpening the stainless steel blade.
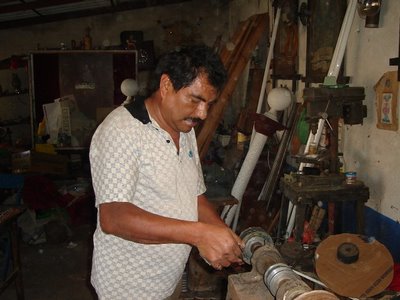
Angel Aguilar is an artist. He works with steel. He makes cutlery, knives and swords. Angel uses the 16th century techniques made famous in Toledo, Spain. These knife and sword making techniques were brought to New Spain in the 1500’s by the Dominican Friars and taught to the Zapotecs. The indigenous Zapotecs then were put to work making knives, swords, tools and implements for the Spaniards.
Angel Aguilar was taught these old processes by his uncle, Ricardo Guzmán, who began learning the Toledo techniques at the age of 8 years from his father. Ricardo Guzmán lived to the age of 110 and Angel says he worked up until his last days. 100 years of sword and knife making from one man.
Angel began to learn the art from his uncle at the age of 10 and now, at the age of 49, has been doing it for 39 years. Angel’s uncle Ricardo was taught the techniques by his father who was taught by his father etc. We are talking about almost 500 years of knife and sword making in one family. And it will continue because Angel is teaching two of his nephews the art.
Angel use 3 different techniques to temper his blades. In this post we’ll examine the technique from Toledo, Spain, which the Dominican Friars taught Angel’s ancestors in the mid 1500’s.
The Materials
Angel makes better blades than his forefathers or the Spanish ever dreamed of making because he starts out with better steel. He uses automotive and truck leaf spring steel. He makes his hilts and pommels out of bronze. Not brass, but bronze. Bronze as in Achilles versus Hector outside the walls of Troy. Bronze as in Alexander the Great hacking through the Gordian Knot. His best handles are made of ironwood. He applies no finish of any kind to the handles. He uses another, flame hardened, piece of ironwood to smooth and polish each handle.
He also offers handles in bone, bull horn, antler and ivory. For a working blade that a hunter, fisherman or woodsman would want, the ironwood handles are by far the best. He picked up a finished knife with its ironwood handle, pulled out a smaller knife and then proceed to scuff the just finished knife’s handle. He basically ruined its appearance right before my horrified eyes. He then picked up his flame hardened "polishing stick" and in a couple of minutes had polished out all of the scratches with which he had just marred the handle. Amazin’.
The Forming
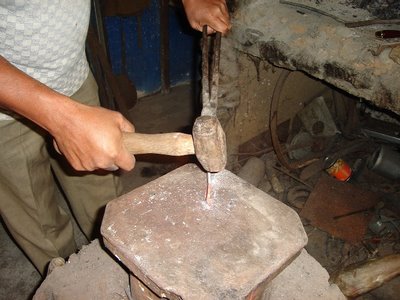
Angel does not cut the leaf spring steel to shape. He only cuts it to approximate length. He does this with a hacksaw. It takes him about 1 1/2 hours of sawing to cut a piece of leaf spring to length. He then places the steel in his forge and heats it to about 4000ºF. He begins to hammer the blade into the shape he wants. He repeatedly heats and hammers until he has formed the blade that he wants. If you look at his knives and swords, especially the knives, it is hard to imagine how he hammers some of the finer detailed shapes. But he has about 30 different sized hammers and chisels that he uses.
The Tempering
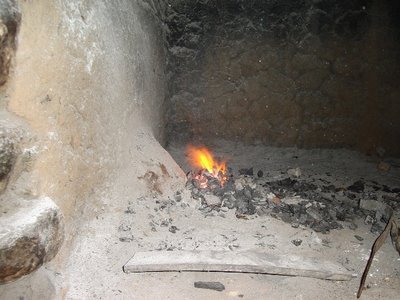
Now comes the tempering. He reheats the blade very slowly to one of three colors which will determine its final temper. When the blade has taken on a golden (dorado) color, he quenches it in oil. This temper is used for knives up to about 30 cm in length, but no more. At this temper, the blade is very hard and will hold the best edge. It will be just flexible enough to withstand heavy use, such as gutting and skinning deer or filleting and de-scaling fish. I also use my big Bowie to split wood, but I’m an idiot.
For swords and machetes, as well as any blade longer than 30 cm, Angel continues to slowly heat the blade until it turns a violet color. After quenching this blade in oil, he has a blade with just a bit more flexibility than with the previous process. That’s because a longer blade must be a bit more flexible so as not to snap during use. This will be a tough blade that will hold an good edge but not as hard as the blades tempered through the “dorado” stage.
For rapiers, sabers and foils, Angel continues to slowly increase the temperature of the blade until it turns a bluish color. Then this blade is oil quenched. This is the most flexible of all the blades. He picked up a thin bladed saber, bent the blade 360º (a full circle) and then released the tip and it snapped back into shape.
The finishing
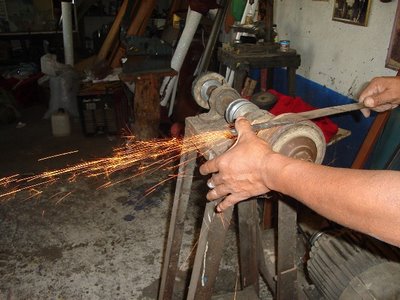
After the tempering process, Angel goes to work on the finish. He begins to grind out the hammer marks, repeatedly cooling the blade in water to avoid modifying the temper that he just spent a week in getting right. He uses an emery wheel on an electric grinder in place of the granite wheels and hand cranked grinders used by the 16th century Spaniards.
After he is satisfied with the rough finish and convinced that the temper is still good, he moves to the next step. He switches to a cotton wheel which he impregnates with carnauba wax. He sprinkles on a course volcanic pumice and polishes out all of the marks left by the emery wheel. He repeats this process through 5 different sizes, or grits, of volcanic pumice, each time polishing out the marks left by the preceding step.
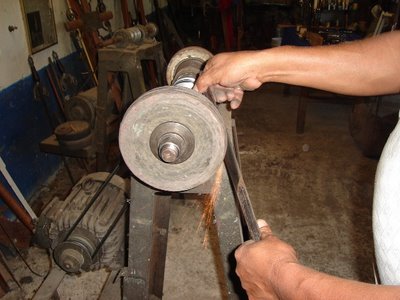
He changes wheels yet again, replacing the cotton wheel with one made of cardboard. He makes these wheels himself and tells me he knows of no other knife and sword makers -- cuchilleros – who follow this step. He impregnates the cardboard wheel with carnauba wax which contains Teflon. Another modern convenience not available to the sword makers in 16th century Toledo, Spain. The wax acts as a carrier which deposits and then holds the Teflon in the microscopic pits on the surface of the steel. This helps to make the blade water resistant.
Note: The blade is not water proof. It is not stainless steel. Some care and maintenance is required but Angel has that worked out pretty well, too. He says that a cotton rag and Brasso will repair any damage to the blade caused by forgetting to oil it once a month. As for the oil, Angel says you can use anything from olive oil from your wife’s kitchen to used motor oil and anything in between.Angel then forms the bronze hilt and pommel around the tang of the blade, again all by hand. He polishes the bronze in much the same fashion as the blade, although it goes much quicker now because bronze is considerably softer than the tempered steel. That’s how the Greeks lost the Mediterranean to the Romans. Roman steel against Greek bronze.
He uses this stage to help balance the knife. He’ll add or subtract as much heavy bronze as is necessary to balance the knife. Some of his knives have interesting eagles heads or other animal heads hand cut into the pommels. He did this because he had to add so much bronze to get the balance he wanted that he had to decorate the extra bronze. If I hadn’t told you that, you would think it was all planned in advance.
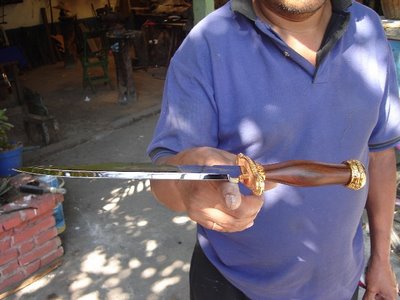
Then he hand carves and polishes the handle. He does not use any adhesives to attach the handle to the tang. It is a force fit, whether the handle be of wood, bone, antler or ivory.
Note: I don’t know where he gets his ivory and I’m not going to ask. It is, however, ivory and not mother-of-pearl. I would not recommend trying to import an ivory handled knife or sword. There are some very strict laws governing the international ivory trade and if you cannot prove that the ivory on your knife or sword came from Inuit who hunted down walrus or from old piano keys or billiard balls, US Customs will confiscate said blade. Then they’ll come looking for me. Besides, ivory turns yellow with age, especially if exposed to sunlight.Now he finish polishes the blade, again using the cardboard wheel with the carnauba wax and Teflon.
UPDATE I: Angel then strops the blade edge using a leather strop, just like a barber does, or at least used to do, before shaving someone. And the blade is finished.
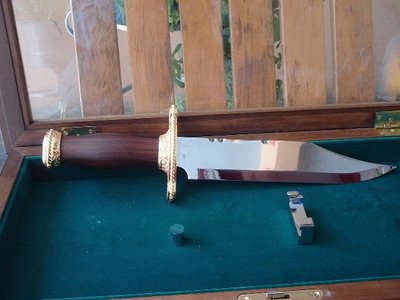
UPDATE II:
10" blade, overall length 15 1/2" - $350
9" blade, overall length 14 1/2" - $325
8" blade, overall length 13 1/2" - $300
1.5 to 2 weeks
Etching and Decorating
While I was there today, a Mexican Army general waltzed in with his four bodyguards. He bought an antler handled knife with a 10 7/8 inch blade. It was the first knife Angel had sold all week. I was looked upon with great favor later as having brought him good luck. The general then paid Angel $75 US extra to do some artwork on the blade. The Mexican Army general had more US currency in his pocket than did I. Hmmm.
Angel makes what I would call a “masking paint”. It’s a mixture of tar, gasoline, paint thinner and some other secret ingredients that he would not divulge. Probably a little kryptonite. He free hand draws on the blade with an old style ink pen. He can put just about anything on the blade that you would want. For the general he wrote the date, the general’s army group, the generals name and rank on one side of the blade. On the other he drew a miniature military fort and a soldier firing a rifle. Then he added some flowery curlicues that he thought the general would like.
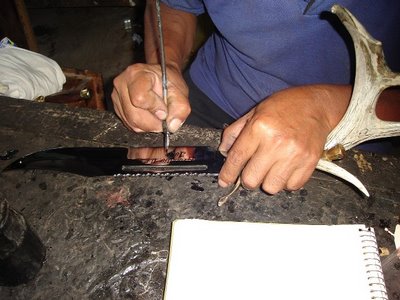
While he did all this the general helped himself to a couple of cans of Modelo that Angel’s wife had raced to the store to buy. When the general was satisfied with the accuracy of the data and the other decorations painted on the knife, he left with his entourage, promising to return tomorrow to pick up his knife. Angel then painted the cutting edges and the back of the knife to protect them. Angel proceeded to hang the blade in a container of muriatic acid which will etch the surface of the blade, everywhere except the painted areas. When the blade is finished, it will have all of Angel’s design in relief.
I have seen this technique used by other knife and sword makers. What is much more common, however, is the use of high speed grinding tools, like the Dremel, to grind a design into the steel. Also used are pantographs or other duplicating type machines. If you’re going to want lettering done on your knife or sword, it would be best to opt for script or maybe something very Gothic. If you want near perfect Times New Roman font, Angel is not your man.
Also, grinding on a knife blade can mess up the temper. The muriatic acid that Angel uses is hydrochloric acid watered down to about 30%. Angel cuts it another half, to about 15%. With all cutting surfaces masked as well as the back of the blade, the acid etching process has no effect on the temper or the fine edge that has been left on the blade.
Tomorrow, when the background, or relief, around his design is etched into the steel, Angel will polish the masking paint away, again using the carnauba wax/Teflon combination with the cardboard polishing wheels.
And that is the Toledo, Spain process for hammering and tempering a knife or sword. Tomorrow, I’ll write another post explaining the Japanese technique for putting a crystallized edge on daito and shoto (long and short) Japanese swords. This technique was taught to Angel’s uncle Ricardo Guzmán by a Japanese sword maker who came to Mexico back in the 30’s. Angel does not know why the man was here or what became of him.
Hold onto your socks because this technique is extremely expensive. It takes Angel about 6 weeks to make a daito and he’ll throw away as many as half a dozen blades before he gets the one he wants.
There is yet another technique known as Damascus steel. I’ll try to write about it tomorrow, also. Here’s a hint. This process is so expensive and time consuming that it requires 2 months of work. It was so expensive even back in the days when the Arabs used slaves and the Spaniards used unpaid Zapotecs that only Arab royalty, the King of Spain and the Viceroy of New Spain could afford such a blade.
But that’s for tomorrow.
for art, gifts and collectibles -- all hand made
by Mexican indigenous artists.
Thanks!
Cross posted at Mark in Mexico
TAGS: Oaxaca, Mexico, Oaxaca teachers strike, Pale Horse Galleries, gifts, collectibles, Mexican arts and crafts, knives and swords

The Pale Horse
2 Comments:
excelent
I have two long shorts and six different size knives all etched and made by Angel interested in finding out more if possible and maybe the value
Post a Comment
<< Home